A letter from Carl J. Berg, Ph.D. – Senior Scientist Kauai Chapter, Surfrider Foundation
The Kauai Chapter of the Surfrider Foundation removes and weighs approximately 5 metric tons of marine debris from the coastline of the Hawaiian Island of Kauai each month. The Hawaiian Islands serve as a stationary sieve, catching marine debris spun off the great garbage patch by the north Pacific gyre.
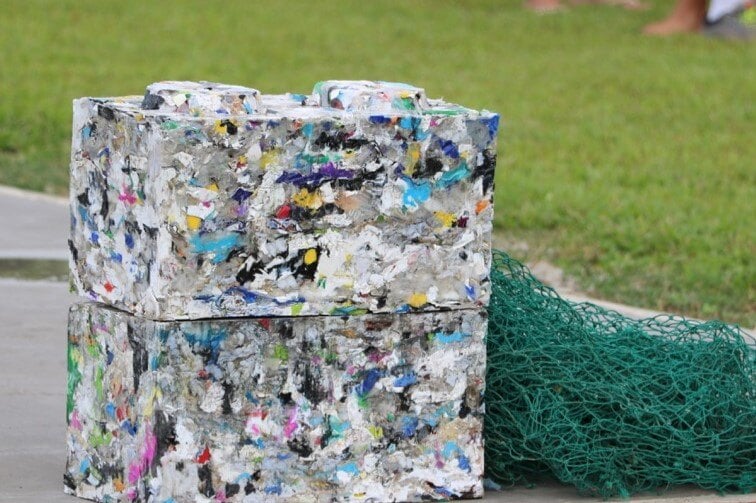
Currently 56% of that weight consists of derelict fishing gear (nets, ropes, lines) and 29% hard plastic associated with derelict fishing gear (buoys, floats, baskets). For that reason, we have joined in the Global Ghost Gear Initiative (GGGI) efforts to reduce this most deadly type of marine pollution.
As the chapter became more efficient at debris removal, we became acutely aware of the problems of disposal of this predominantly plastic waste. We joined others in Hawaii’s Nets-to-Energy program until we discovered the levels of heat, greenhouse gas (GHG) and toxic gas emissions coming from the Honolulu incineration facility. In searching for alternative methods of disposal we had to confront the basic toxic nature of plastics and the effects of recycling on global climate change.
We want to remove plastic from the environment while at the same time capitalizing on the intrinsic value of plastic. We partnered with an innovative new company, ByFusion, in testing the feasibility of taking a sampling of Kauai’s derelict fishing gear and fashioning it, along with plastic domestic waste, into building blocks. The plastic is shredded, steam cleaned and compressed into ByBlocks. The ByFusion Byblocks are the general shape of a Lego and size of the conventional cement building blocks they are designed to replace. Each Byblock weighs approximately 10 kg and contains the equivalent of 555 plastic drinking water bottles (Figure 1).
Surfrider joined with ByFusion and Island School in the building of a 12’ x 20’ athletic pavilion alongside the school’s outdoor basketball court. This is the first permanent structure built of ByBlocks in the world. The building was of post-and-beam construction, with the non-supporting walls made of 216 ByBlocks (~2.2 mt) (Figure 2). The building met appropriate building codes, was government approved, and built by licensed contractors pleased to be the first to utilize this remarkable new material.
Figure 2.
Construction of the ByBlock walls took only a day, once the threaded rebar had been anchored in the concrete foundation. Inter-locking ByBlocks were slipped over the rebar into place and the walls secured by inserting a top plate and tightening down on the threaded rebar. The walls were then covered with stucco for aesthetics, to prevent UV degradation of the plastics, and to cut emission of GHGs (Figure 3, 4). The replacement of cement blocks by ByBlocks helps reduce material and labor costs and also GHG production.
Figure 3.
Figure 4.
The use of ByFusion technology seems ideally suited for islands and remote areas that can utilize abundant plastic marine debris and domestic waste in the production of a versatile building material that can be used locally.
Five years later, we are thrilled to report, the pavilion is still in like-new condition!